Hydroxypropyl methyl cellulose can improve the resistance to dispersion of cement mortar
Anti - dispersion is an important technical index to measure the quality of anti - dispersant.
Hydroxypropyl methyl cellulose is a kind of water-soluble polymer compound, also known as water-soluble resin or water-soluble polymer, is to increase the viscosity of mixed water, increase the consistency of the mixture, is a kind of hydrophilic polymer material, can be dissolved in water to form solution or dispersion.The experiment shows that when the amount of naphthalene superplasticizer increases, adding superplasticizer can reduce the anti-dispersibility of fresh cement mortar.This is because naphthalene superplasticizer is a surfactant.When the superplasticizer is added to the mortar, the superplasticizer is oriented on the surface of cement particles, making the surface of cement particles have the same charge. This electrical repulsion causes the flocculation structure formed by cement particles to be broken down, and the structure of water is released, which will lead to the loss of part of cement.At the same time, it was found that with the increase of HPMC content, the dispersion resistance of fresh cement mortar was also getting better and better.
Strength characteristics of concrete:
Highway bridge foundation engineering adopts HPMC underwater non-dispersive concrete admixture, design strength grade C25.Basic tests, cement dosage is 400 kg, 25 kg/m3, mixed with silicon powder smoke HP 0.6% cement the best dosage of cement, water cement ratio of 0.42, sand ratio 40%, naphthalene water reducing agent yield of 8%, cement concrete specimens 28 d, the average intensity of 42.6 MPa, underwater concrete 28 d drop height 60 mm, the average intensity of 36.4 MPa, the water with the air of the concrete forming strength ratio of 84.8%, the effect is more significant.
1. The addition of HPMC has obvious retarding effect on mortar mixture.With the increase of HPMC content, the setting time of mortar is prolonged.Under the same amount of HPMC, the time of underwater forming mortar is longer than that of air condensation.This function is great for pumping underwater concrete.
2. Fresh cement mortar mixed with hydroxypropyl methyl cellulose has good bonding performance and almost no bleeding.
3. The content of
HPMC cellulose and the amount of water used for mortar shall first drop and then rise.
4. The addition of efficient water reducer improves the water demand of mortar, but it must be properly controlled.Otherwise, the dispersion resistance of fresh cement mortar is sometimes reduced.
5. The structure of cement paste mixed with HPMC is not much different from that of blank samples.The difference of paste structure and density was not obvious.The 28d underwater forming specimen is slightly brittle.The main reason is that the addition of HPMC greatly reduces the loss and dispersion of cement during pouring, and at the same time reduces the compactness of cement.Ensure the underwater dispersion effect in the project, as the amount of HPMC is minimized.
6. Adding HPMC underwater non-dispersive concrete additives, dosage control is conducive to the strength, the test shows that the molding concrete and air molding strength ratio of 84.8%, the effect is more obvious.
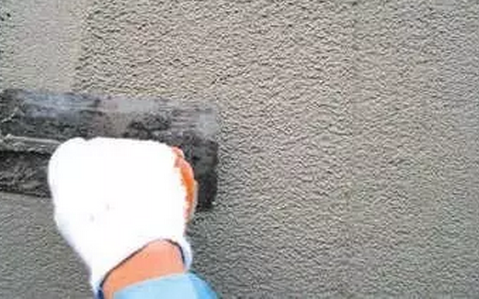